10-1200ml Aerosol Production Line
1. This machine operates in a stable and reliable manner with fewer failures and a longer lifespan.
2. It has higher efficiency and leads to lower labor costs.
3. It features higher precision and more stable filling quality.
4. The main pneumatic components and seal rings are of international - quality products, thus having excellent reliability and abrasion - resistance.
5. The conveyor of the production line adopts an explosion - proof variable - speed motor, and the rest is driven by compressed air, so it has high safety.
6. It has a one - key lifting function, which greatly boosts production and enables the changing of the star wheel speed.
High Speed Aerosol Filling MachinePRODUCT PARAMETERS
Technical Parameter |
Description |
Voltage |
380V/50HZ( can be customized ) |
Dimension(L*W*H) |
22000*4000*2000mm |
Production speed |
130-150 cans/min |
Propellant Type |
The type of propellant used in the aerosol product (e.g., LPG, DME, N₂, CO₂, R134a, etc) |
Noise control |
≤80 dB |
Can Type |
Tinplate can or aluminum can |
Driven Type |
Pneumatic control |
Material |
SS304 ( some parts can be SS316) |
Warranty |
1 year |
Key Selling Points |
High speed fully automatic high production |
Maintenance Requirements |
Recommended maintenance procedures and schedules |
Certifications and Standards |
CE&ISO9001 |
Filling accuracy |
≤±1% |
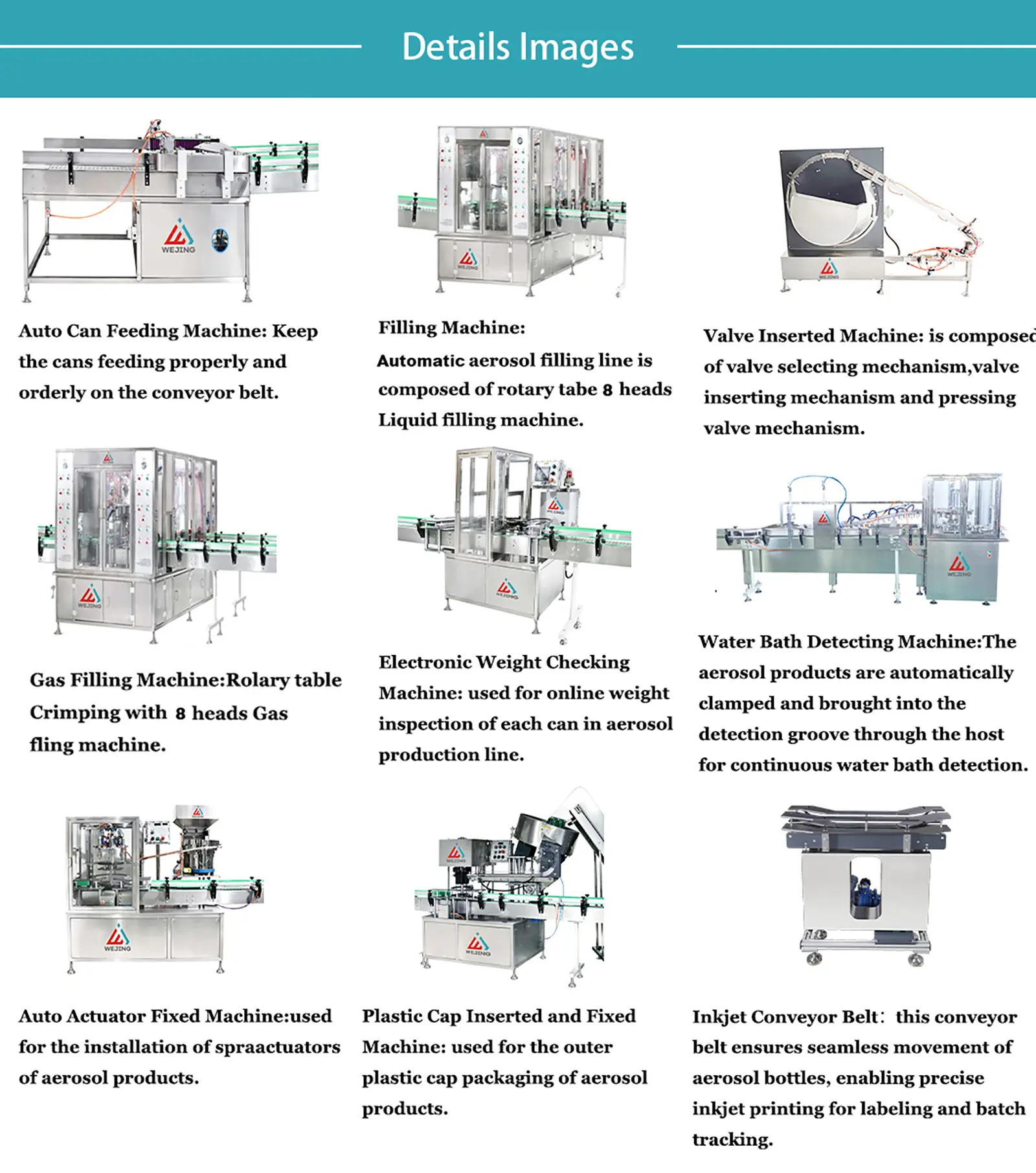
Product Applications
This production line is characterized by high precision and high efficiency. It can fill one - inch tinplate and aluminum cans that are applicable internationally. Moreover, it is suitable for filling oil, water, latex, solvent and other substances with medium viscosity. It can also be used to fill propellants such as DME, LPG, 134a, N2, CO2. In addition, it is applied to fill liquids in the chemical, cosmetic, food and medical industries.
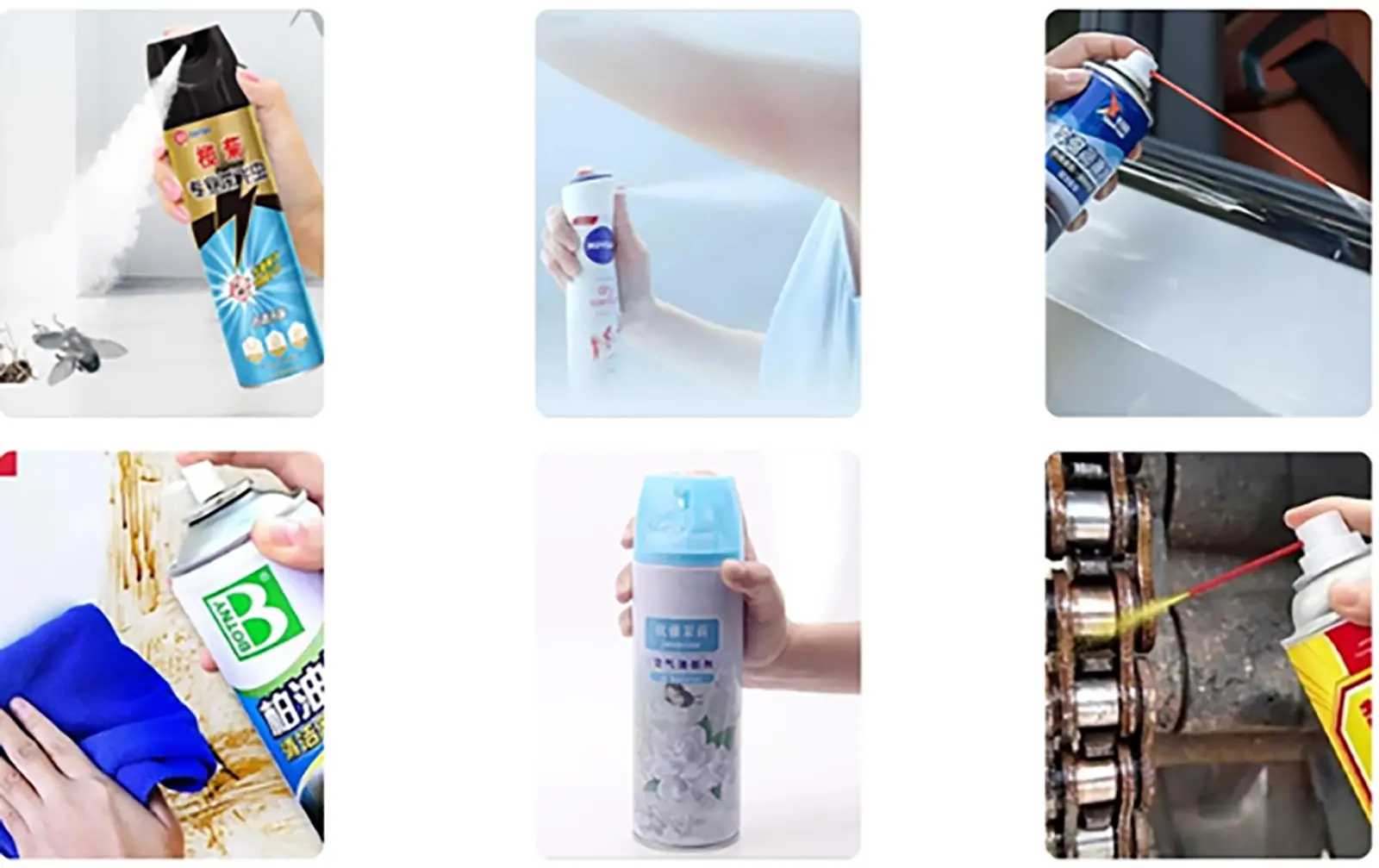
Operate Guide
1. Gather materials: Confirm the aerosol cans and propellants are the correct type and amount.
2. Adjust settings: Set filling speed, pressure, and temperature as per product details.
3. Start line: Turn on the equipment and watch to ensure smooth running.
4. Inspect filled cans: Check for leaks, fill levels, and defects.
5. Clean & maintain: Regularly clean and lubricate the line to extend its life.
2. Adjust settings: Set filling speed, pressure, and temperature as per product details.
3. Start line: Turn on the equipment and watch to ensure smooth running.
4. Inspect filled cans: Check for leaks, fill levels, and defects.
5. Clean & maintain: Regularly clean and lubricate the line to extend its life.