Aerosol Insecticide Filling Sealing Machine
This equipment is equipped with 8 filling heads (10 can be customized), which can perform filling operations simultaneously, greatly improving production efficiency. It is easy to operate and can accurately adjust the filling volume and filling speed through an advanced control system. The fully automatic aerosol filling machine is suitable for multiple industries such as daily chemical, pharmaceutical, and food, and can fill various products such as air fresheners, insecticides, and oil agents. It has the characteristics of high stability, precise filling, and easy maintenance, providing reliable guarantee for large-scale production of enterprises.
High Speed Aerosol Filling MachinePRODUCT PARAMETERS
Production speed |
130-150 cans/min |
Filling volume |
30-1200ml |
Filling accuracy |
≤Filling accuracy |
Noise control |
≤80 dB |
Material |
SS304 ( some parts can be SS316) |
Voltage |
380V/50HZ( can be customized ) |
Driven Type |
Pneumatic control |
Packaging Type |
Tinplate can or aluminum can |
Propellant Type |
The type of propellant used in the aerosol product (e.g., LPG, DME, N2, CO2, R134a, etc) |
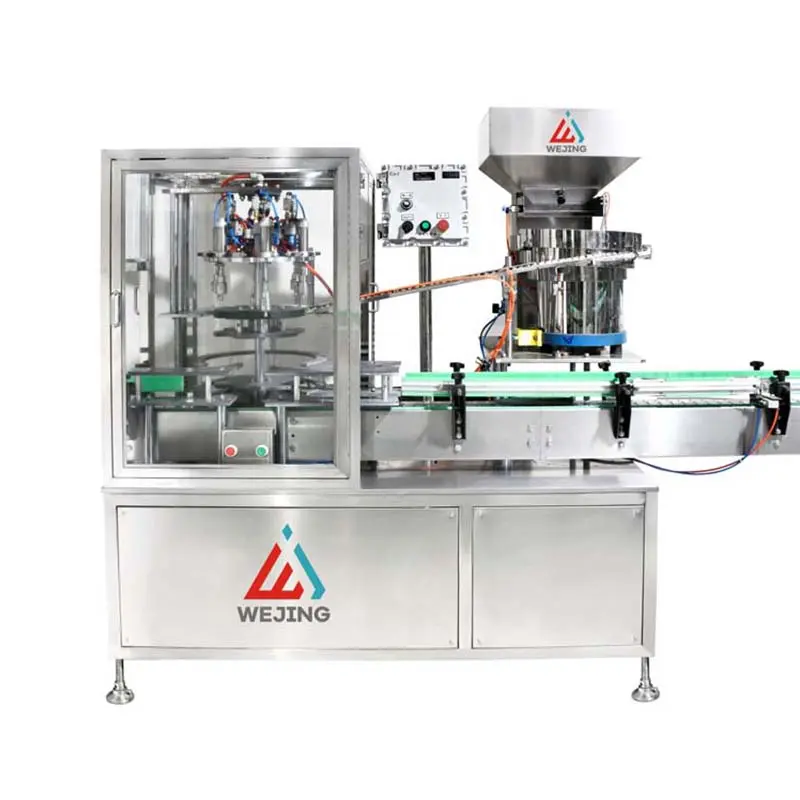
High - efficiency production speed
It can produce 130 - 150 cans each minute, fulfilling the requirements of medium - to large - scale production and enhancing efficiency.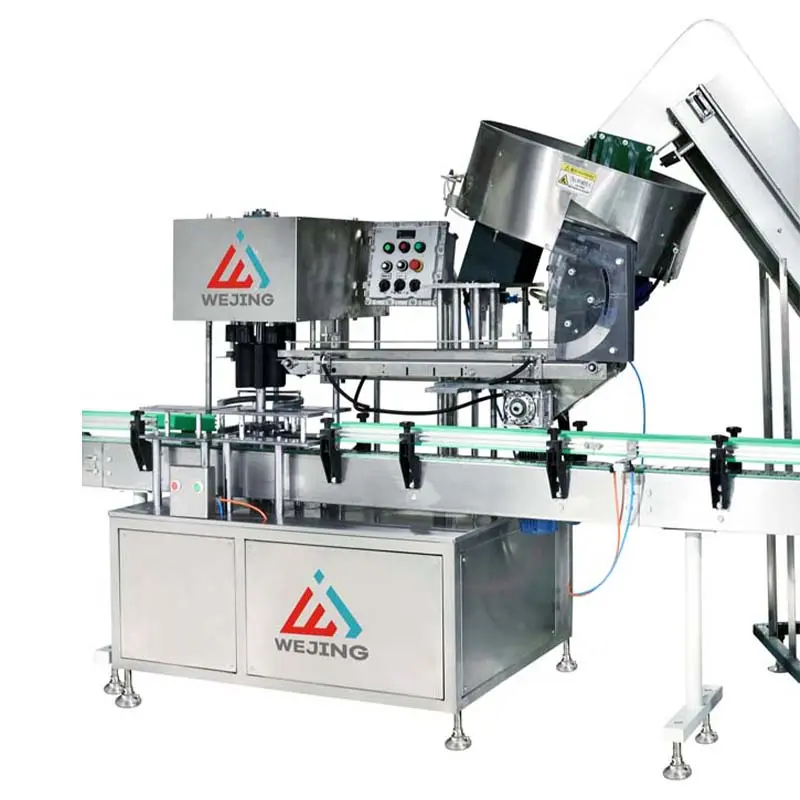
Versatile filling capacity
Ranging from 30 to 1200ml.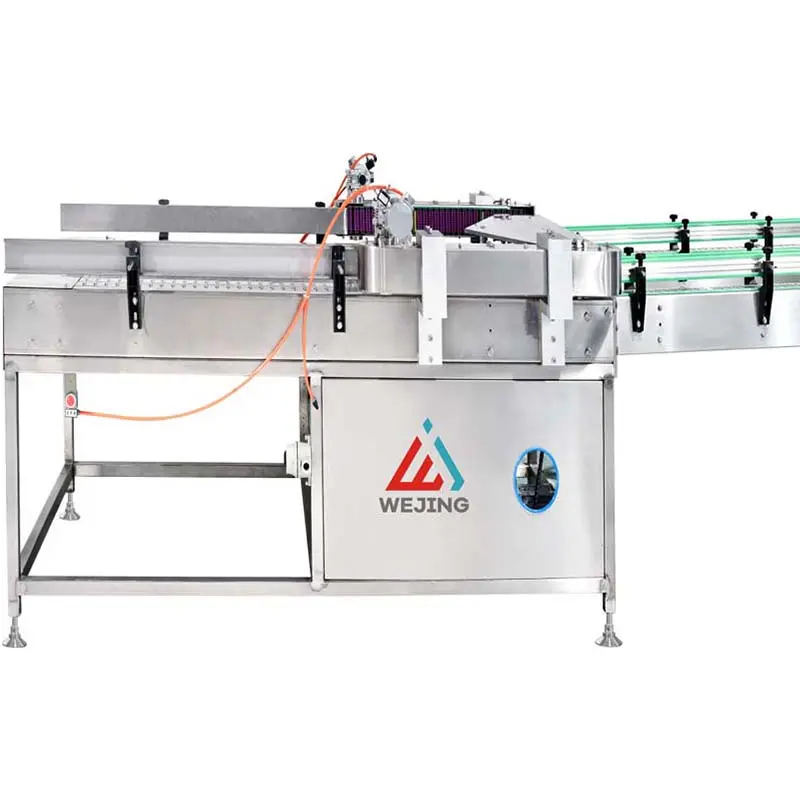
Multiple - station setup
Equipped with eight filling heads to boost parallel processing and efficiency while enhancing stability.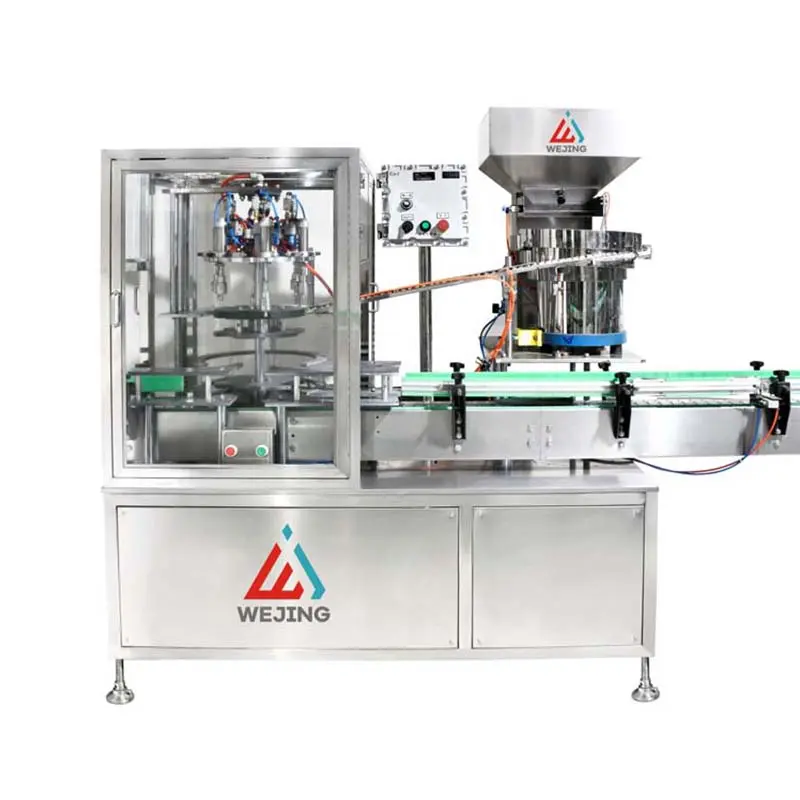
User - friendly operation and maintenance
Both operation and maintenance are convenient, cutting down on personnel reliance and costs.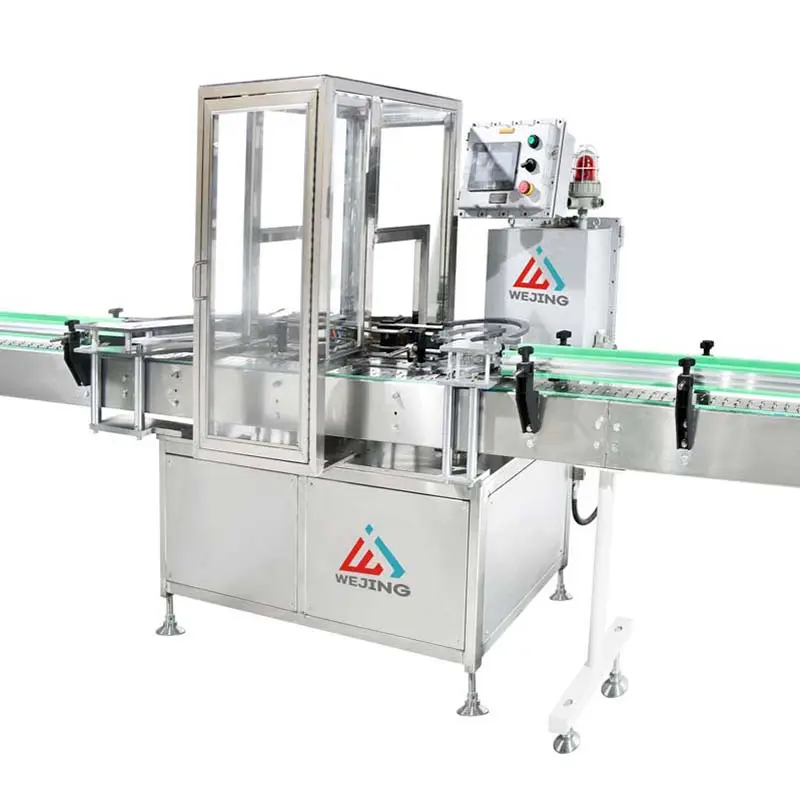
Precise high - precision control
Guarantee the accurate volume of filling, improving product uniformity and the pass rate.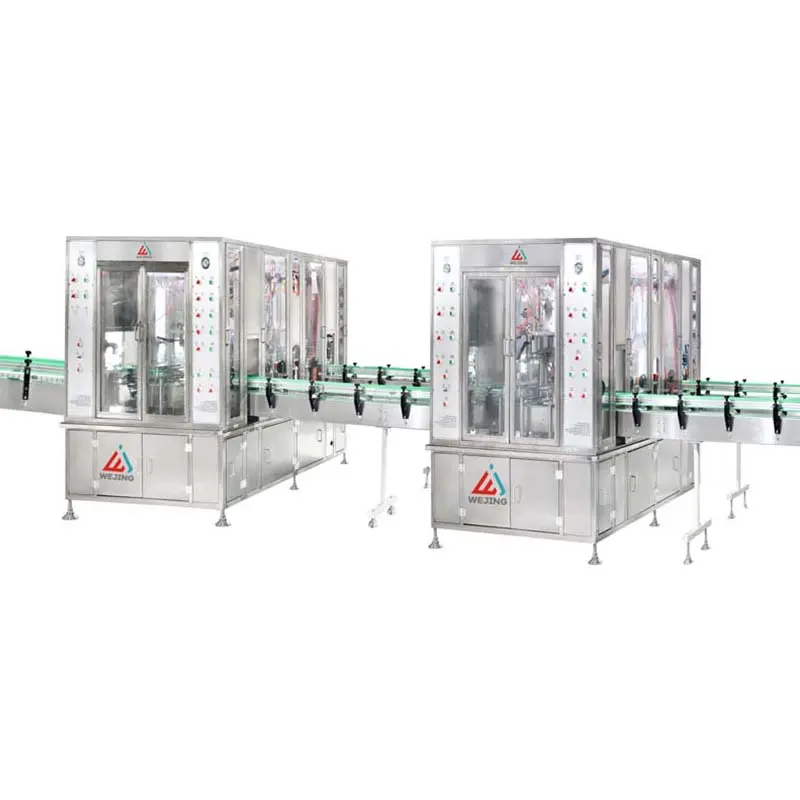
Excellent compatibility
It fits different specifications of aerosol cans and has great universality.Product Applications
1. Personal care products: hair dye, body fragrance, insect repellent, sunscreen, hair removal agent, etc.
2. Household products: such as furniture polishing wax, household cleaner, air freshener, pet spray, plant spray, household fire extinguisher, etc.
3. Sanitary products: such as toothpaste, cleaning agents, etc.
4. Food: such as cream toppers, concentrated drinks, cooking seasonings, juices, sauces, etc
5. Industrial supplies: such as sealing agents, grease and lubricants, industrial oils, etc.
6. Automotive supplies: such as adhesives, sealants, polishes, combustion injector cleaning agents, barrier creams, paints, etc.
2. Household products: such as furniture polishing wax, household cleaner, air freshener, pet spray, plant spray, household fire extinguisher, etc.
3. Sanitary products: such as toothpaste, cleaning agents, etc.
4. Food: such as cream toppers, concentrated drinks, cooking seasonings, juices, sauces, etc
5. Industrial supplies: such as sealing agents, grease and lubricants, industrial oils, etc.
6. Automotive supplies: such as adhesives, sealants, polishes, combustion injector cleaning agents, barrier creams, paints, etc.
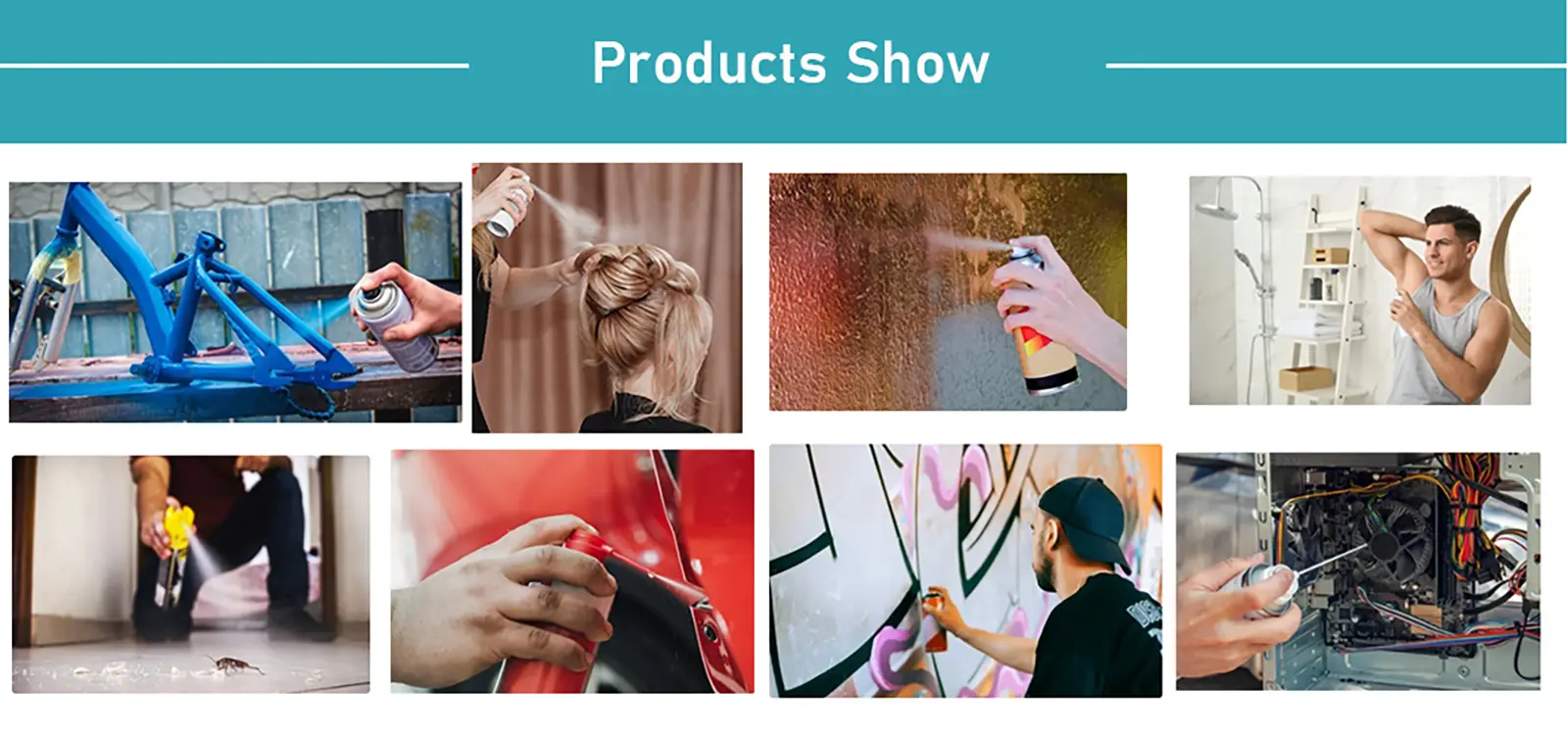
After Sales Service
1. Installation and debugging. Professional personnel can be arranged to install equipment on-site or provide online guidance
2. Operation training. Provide comprehensive training for customer operators, including operating methods, daily maintenance, and troubleshooting skills, to ensure proficiency.
3. Maintenance response. Promise to respond promptly upon receiving a fault report, arrange for technical personnel to go for repairs in a timely manner, and reduce downtime.
4. Accessory supply. Long term provision of original factory accessories to ensure the quality of accessories matches the equipment, ensuring stable operation of the equipment.
5. Regular follow-up visits. After sales personnel regularly visit customers to understand equipment usage, collect feedback, and continuously improve services.
2. Operation training. Provide comprehensive training for customer operators, including operating methods, daily maintenance, and troubleshooting skills, to ensure proficiency.
3. Maintenance response. Promise to respond promptly upon receiving a fault report, arrange for technical personnel to go for repairs in a timely manner, and reduce downtime.
4. Accessory supply. Long term provision of original factory accessories to ensure the quality of accessories matches the equipment, ensuring stable operation of the equipment.
5. Regular follow-up visits. After sales personnel regularly visit customers to understand equipment usage, collect feedback, and continuously improve services.