Automatic Bag On Valve Filling Machine
Automatic Bag On Valve Aerosol Filling MachinePRODUCT PARAMETERS
Filling capacity (cans/min) |
45-60cans/min |
Liquid filling volume (ml) |
10-300ml/head |
Gas filling accuracy |
≤±1% |
Liquid filling accuracy |
≤±1% |
Applicable cans diameter (mm) |
35-70 ( can be customized) |
Applicable cans height (mm) |
70-300 ( can be customized) |
Applicable valve (mm) |
25.4 (1 inch) |
Propellant |
N2, compressed air |
Max gas consumption (m3/min) |
6m3/min |
Power (KW) |
AC 380V/50HZ |
Air source |
0.6-0.7Mpa |
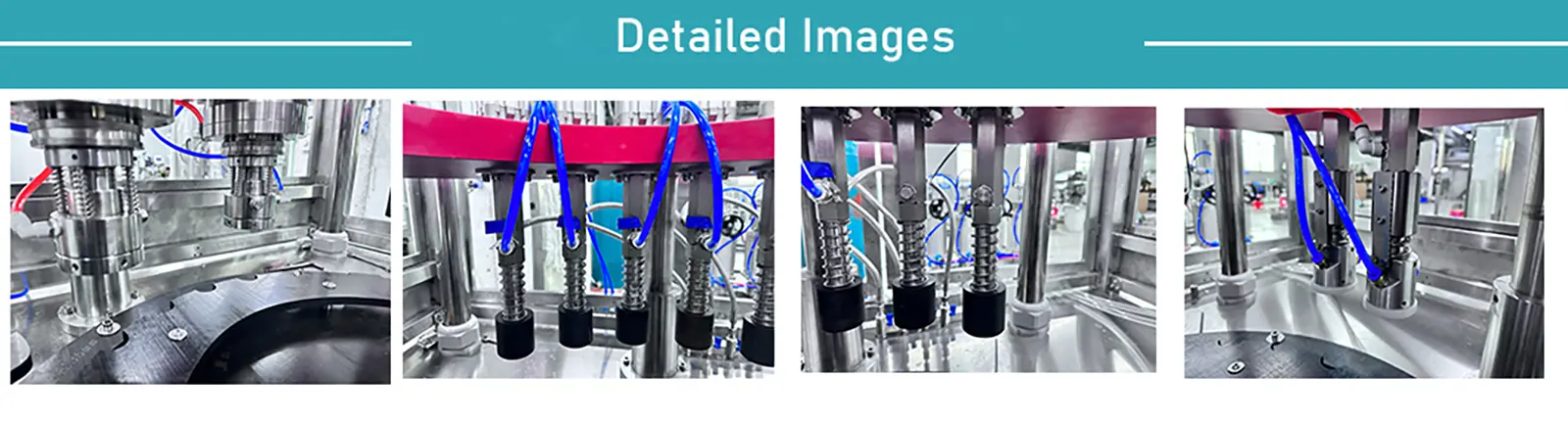
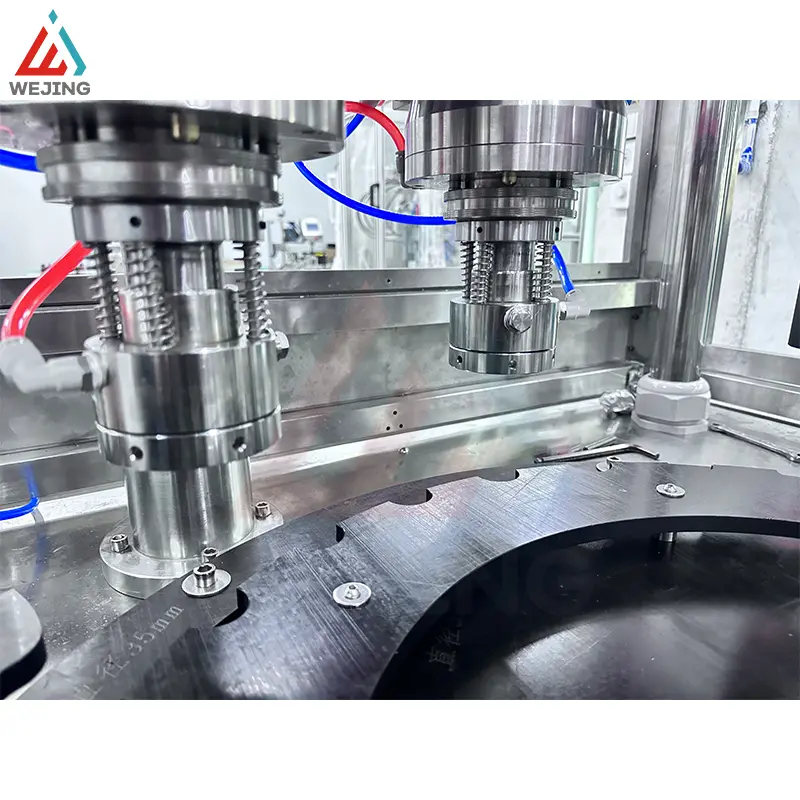
1. Multifunctionality: It integrates multiple functions such as inflation, liquid filling, pressure measurement, and cleaning, and can meet the production needs of binary aerosol products.
2. Efficient production: The speed can reach 45-60 cans/minute, which can achieve high production efficiency and is suitable for large-scale production.
3. Precise filling: The filling volume is between 30-1200ml, which can be adjusted precisely according to different product requirements to ensure filling accuracy.
2. Efficient production: The speed can reach 45-60 cans/minute, which can achieve high production efficiency and is suitable for large-scale production.
3. Precise filling: The filling volume is between 30-1200ml, which can be adjusted precisely according to different product requirements to ensure filling accuracy.
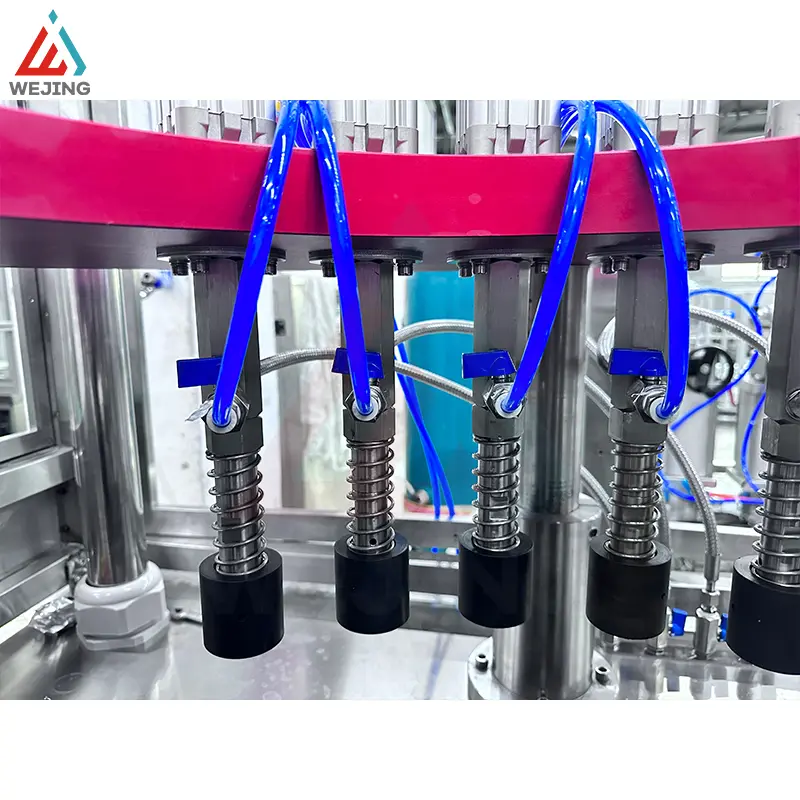
4. Dual inflation heads: Improve inflation efficiency, ensure stability and consistency of gas filling.
5. Multiple infusion heads: Increase infusion speed while ensuring uniformity of infusion.
6. Pressure gauge head: Real time monitoring of the pressure inside the aerosol can to ensure product quality and safety.
7. Cleaning hair: Clean the equipment during the production process to maintain cleanliness and hygiene, and reduce cross contamination.
5. Multiple infusion heads: Increase infusion speed while ensuring uniformity of infusion.
6. Pressure gauge head: Real time monitoring of the pressure inside the aerosol can to ensure product quality and safety.
7. Cleaning hair: Clean the equipment during the production process to maintain cleanliness and hygiene, and reduce cross contamination.
Working Process
1. Put the empty aerosol can onto the conveyor belt and convey it to the inflation station.
2. Two inflation nozzles inflate the aerosol can simultaneously. They inject the necessary gas into the can and conduct the sealing process.
3. The inflated and sealed aerosol can is then conveyed to the filling station.
4. Six filling nozzles perform the filling operation at the same time, precisely pouring the liquid materials into the aerosol can.
After the filling is done, the aerosol can is transported to the pressure - measuring station, where two pressure - measuring nozzles are used to detect the internal pressure of the can.
If the pressure fails to meet the requirements, the equipment will make relevant adjustments or trigger an alarm.
7. Cleaning brushes will clean the aerosol cans.
2. Two inflation nozzles inflate the aerosol can simultaneously. They inject the necessary gas into the can and conduct the sealing process.
3. The inflated and sealed aerosol can is then conveyed to the filling station.
4. Six filling nozzles perform the filling operation at the same time, precisely pouring the liquid materials into the aerosol can.
After the filling is done, the aerosol can is transported to the pressure - measuring station, where two pressure - measuring nozzles are used to detect the internal pressure of the can.
If the pressure fails to meet the requirements, the equipment will make relevant adjustments or trigger an alarm.
7. Cleaning brushes will clean the aerosol cans.
PRODUCT Maintenance
1. Regularly clean the equipment to maintain its cleanliness and hygiene.
2. Check the operation of each component, and replace it promptly if wear or damage is found.
3. Regularly lubricate the equipment to ensure smooth operation of its moving parts.
4. Check the electrical system of the equipment to ensure that the electrical connections are firm, safe, and reliable.
5. Operators should receive training, be familiar with the operation and maintenance methods of the equipment, and strictly follow the operating procedures for operation.
2. Check the operation of each component, and replace it promptly if wear or damage is found.
3. Regularly lubricate the equipment to ensure smooth operation of its moving parts.
4. Check the electrical system of the equipment to ensure that the electrical connections are firm, safe, and reliable.
5. Operators should receive training, be familiar with the operation and maintenance methods of the equipment, and strictly follow the operating procedures for operation.
PRODUCT Applications
Fully automatic binary gas filling line is suitable for filling various products. In the industrial sector, it can be filled with fire extinguisher propellants, refrigeration equipment refrigerants, etc. The medical field is suitable for filling specific medical aerosols. Cosmetic spray that can be filled with binary packaging in the daily chemical field, such as moisturizing spray, makeup setting spray, etc. There are also products such as industrial cleaning agents and foaming agents that use binary packaging.
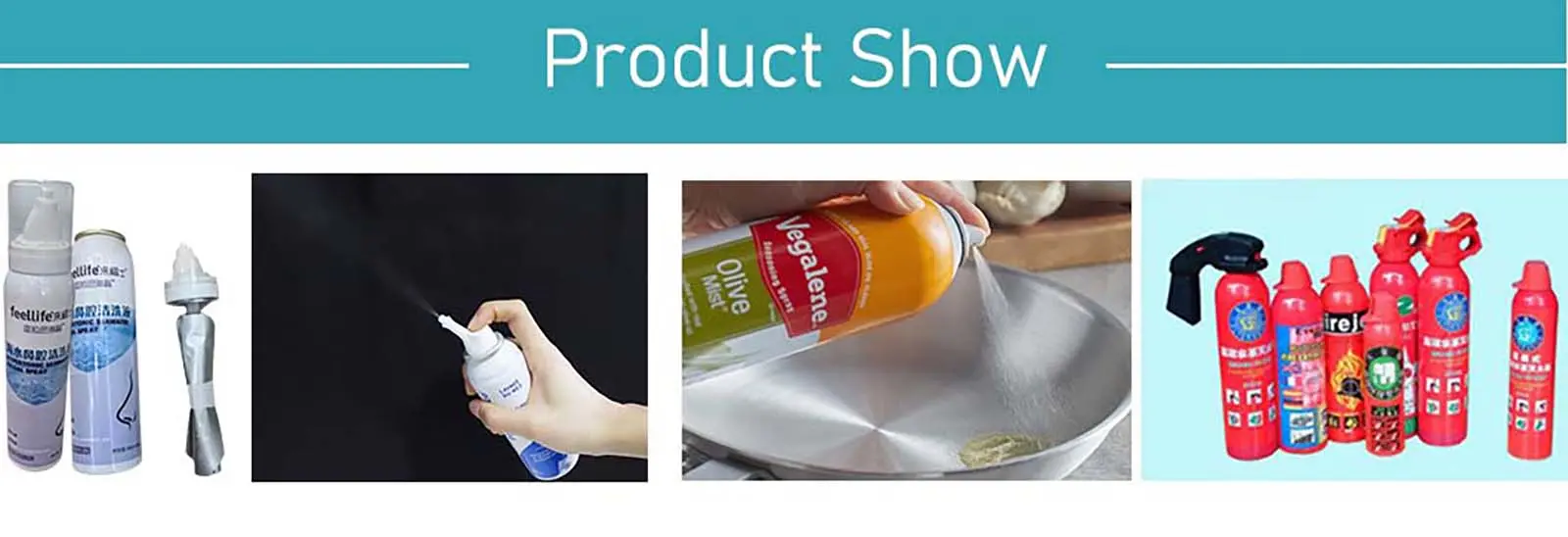